Among other attributes, aluminum promotes mass reduction, improving the performance and efficiency of battery electric vehicles ( BEVs ). In this way, it allows greater autonomy of vehicles — increasingly, is one of the most important attributes for the final consumer.
On the other hand, the introduction of aluminum is beneficial for manufacturers as it allows for more economical production processes. This is because the legislation aims to reduce greenhouse gas (GHG) emissions, thus becoming a driver in the development of electric vehicles , especially in industries with high production.
“ Aluminum is the fastest growing automotive material in terms of content, and as the industry is in the midst of a transition to electrification, decision makers need to have a clear view of the metal's role evolution. The new data quantifies and reaffirms that battery electric vehicles, as they become more and more comprehensive and reduce mass with the application of aluminum, at optimized levels, offer significant cost savings, ” says Blake Zuidema , Director of Development. Technician at Novelis and chairman of the Technical Committee of the Aluminum Transport Group (ATG).
The study was released after the Automotive Aluminum Roadmap and, according to the AA, serves as a tool for decision makers in the automotive industry looking to create value in a rapidly evolving market while also advancing sustainability.
The context of mass reduction in BEVs
In vehicles with an internal combustion engine, the adoption of aluminum is an already widely recognized solution for reducing mass. As an alternative to other heavier metals, aluminum offers greater energy efficiency, being the most economically viable solution to meet legal consumption and emissions requirements .
But when talking about battery electric vehicles ( BEVs , zero emission), the decisive point for the adoption of aluminum, aiming at mass reduction, is another: autonomy with a battery charge. This is generally the preferred solution when the cost is lower compared to adding more batteries for charge storage.
This equation, however, goes beyond the cost of extra batteries versus replacing materials. It is essential to take into account the consequences of adding more battery cells, such as the increase in the total weight of the vehicle and the reduction of the useful internal space – which is often already at the maximum limit. In this case, the solution is really to increase the dimensions of the vehicle.
In addition, to maintain performance with the inevitable increase in weight, it is necessary to resize the powertrain . The vehicle's driving dynamics also change, requiring changes to the suspension system. All of this causes additional costs and can further increase the vehicle's mass.
Another fundamental point is that, generally, the legislation on fuel economy is calculated on the entire fleet of the manufacturer's production - mixing BEVs , hybrids and models with an internal combustion engine.
In other words, the improvement in the energy efficiency of 100% electric vehicles can impact the needs for improvement in the brand's “non-BEV” models. In other words, it may be more economically viable to reduce the mass of BEVs instead of adopting any other solution to improve the efficiency of models equipped with a combustion engine.
Finally, while advances in battery cost reduction and energy storage density are around the corner, the study reveals that aluminum weight-saving solutions are expected to maintain their economic attractiveness for at least the next decade.
The study
Three BEV segments were specified that should, over the next decade, be the focus of the weight reduction cycle in the manufacturers' strategy:
- Sedan/ hatchback , urban compact, four-door. The references used were Hyundai Ioniq and Volkswagen ID.3
- Family crossover, medium, four-door. References: Mustang Mach-E and Audi E- Tron ;
- Pickup (body on chassis), large double cab, four doors. Benchmarking: Ford F-150 (which offers approximate data on the 100% electric F-150 Lighting ) and Rivian R1T.
Three key performance measures were established. The first is the 2020 base of reference vehicles. The others are 2025 and 2030 — whose parameters are based on industry trends observed by the consultancy.
Base model specifications (2020)
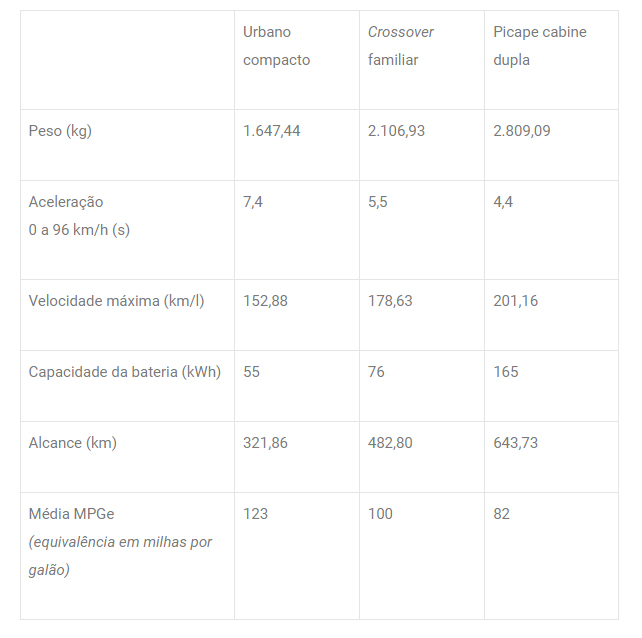
Specifications for 2025
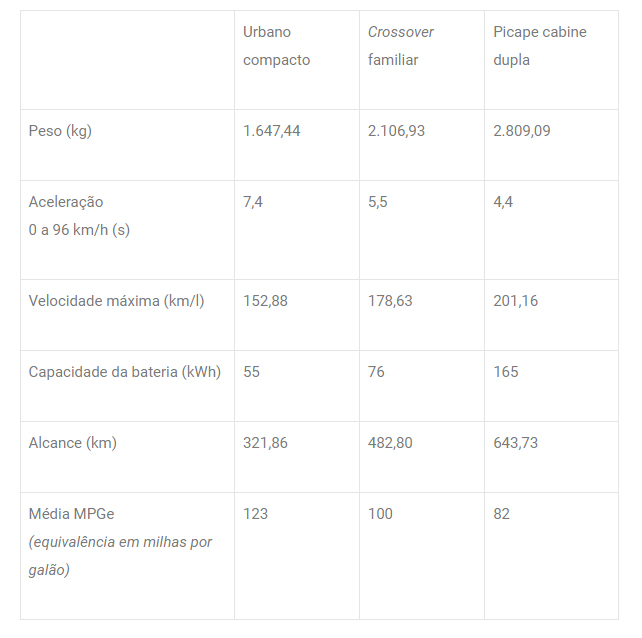
Specifications for 2030
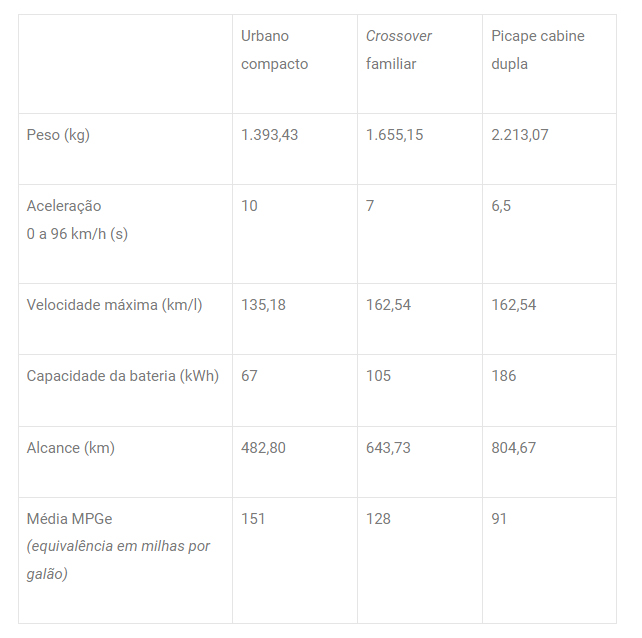
According to the FEV, weight, range and equivalent fuel economy should improve during this period. However, consumers are expected to increasingly value range and cost over ultimate speed and acceleration. Therefore, these last two measures gained tolerance, in order to reduce the final cost of the vehicle.
Substitution of materials
The study also determined a base material composition of the main vehicle systems and components, taking into account the reference models.
Then, a technological evolution roadmap was applied. Materials used in various systems of the three vehicle types today were examined, assessing the potential for material substitution in key components and systems in 2025 and 2030.
According to the study, aluminum was applied to components that are still produced with other materials only when replacement proved appropriate, taking into account both design and performance issues.
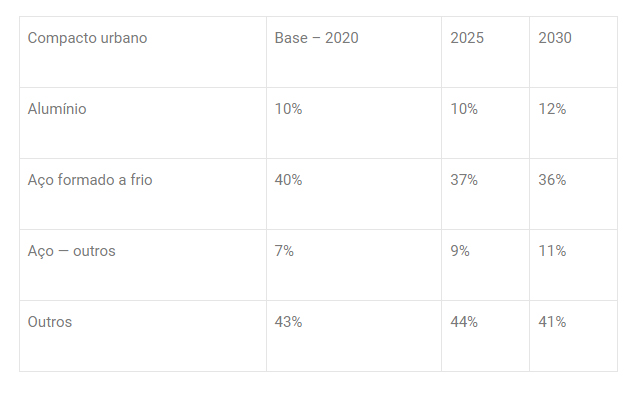
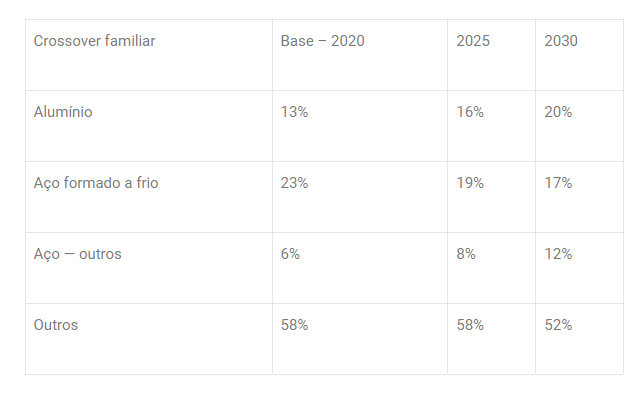
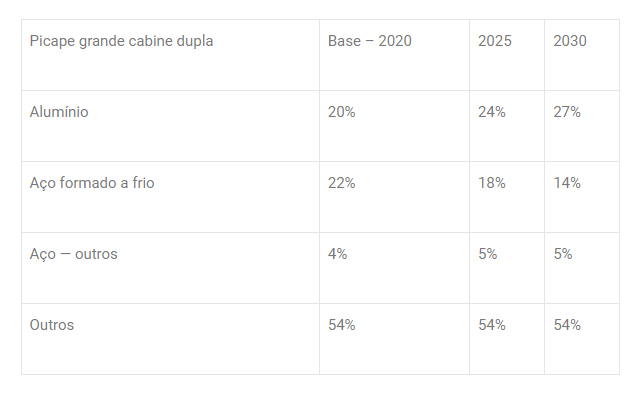
The material baseline composition distribution was developed under the assumption that weight reduction will be driven primarily by the need to decrease battery size to achieve affordable range and assumed factors based on current trends and foreseen future.
More than 40 components were evaluated for their aluminum weight reduction potential — 20 of which were separated for replacement. Overall, selected parts were priced at $6.61 or less per kg of reduced weight.
Weight, cost and impact on BEV efficiency
The weight, cost and average impact of the fuel economy of the BEVs on the average of the fleet, by the replacement with aluminum, were determined by gradually increasing the replacement of the metal in target components, in the 2025 and 2030 scenarios.
The aluminum content was incremented by 5% from the baseline vehicle to 100%. The battery and the size of the electric drive motor have been adjusted to maintain constant performance at the levels chosen for each class of vehicle in each scenario. The “ideal aluminum content” was the one that provided the greatest savings in the total vehicle cost.
For the urban compact in 2025, savings were $62 per vehicle, achieved with 25% aluminum content. Replaced components were skid plates, rotor plates, front and rear floors, doors, seats and crossbars. In total, the weight reduction was 124.5 kg. The average cost/kg of weight saved at this level was US$3.76.
For the 2030 scenario, the optimal cost savings was $74, achieved at 28% aluminum content, with the front suspension conversion. The total weight reduced by replacing aluminum in 2030 was 128.7 kg. The average value per kg saved at this level was US$3.14.
For the 2025 family crossover, the optimal economy of $74 has been achieved, with the vehicle featuring 25% aluminum content. Battery housing, rotor end plates, mid floor, body sides, doors and front brake calipers were all converted. The total weight removed by these replacements was 64.77 kg. The average cost/kg of weight saved was US$ 3.74.
For 2030, optimal cost savings were $76/vehicle, achieved with 42% aluminum content. In this scenario, the lower protection plate and front and rear floors were converted, in addition to the seats. The total weight reduction of all replacements for 2030 was 171.9 kg. The average cost/kg saved at this level was $5.08.
For the pickup , in 2025, the ideal savings was $102/vehicle with 35% aluminum content. The battery housing, front, middle and rear floors, front brake calipers and seats were converted. The total weight reduction was 156.2 kg, giving an average cost/kg saved of US$ 5.81.
Traveling to the 2030 scenario, the ideal savings were US$74/vehicle, achieved with 50% aluminum content. The converted parts were skid plates, fire wall, front bumper and deformation structures, in addition to the front suspension and the front and rear subframes . The total reduction in 2030 was 264.2 kg, with an average cost/kg of weight saved of US$ 6.05.
Regarding the influence of BEV weight reduction on the overall fuel economy of the fleet, the three vehicle segments improved the hypothetical overall fleet fuel from 15.98 to 16.54 km/l in 2025, and from 23.51 to 24.36 km/l in 2030.
This represents improvements in fleet fuel economy of 3% and 4%, respectively , in 2025 and 2030 – a fact that increases the viability of aluminum for car manufacturers.
Conclusions
- The aluminum content of battery electric vehicles is currently higher than in models in the same segment equipped with an internal combustion engine;
- The aluminum content of battery electric vehicles is currently increasing in line with dimensions and performance expectations;
- Despite expected improvements in battery cost and storage density, aluminum solutions for weight reduction are expected to remain economically attractive for at least the next decade;
- Light battery electric vehicles with aluminum offer additional economic benefits when the entire sales fleet is considered, further increasing the feasibility of adopting the metal for weight reduction in 100% electric vehicles.
Source: revistaaluminio.com.br